CPI Lubrication
CPI products used in lubricated compressors are heavily influenced by the oil and the lubrication system; too much is a problem – too little is a problem – inconsistent delivery is a problem. Our experience assisting customers in achieving the goal of reliable lubrication to maintain compressor efficiency and protection have earned us the reputation as an industry leader for introducing the latest technology and expertise for lubrication systems worldwide. By offering the best materials combined with the best lubrication systems and controls we can provide the most consistent performance and life to the compressor user.
CPI designs and manufactures a wide range high quality lubricator pumps that come in various models with several options. The model that's right for you will be the model designed to fit in your lubricator box.
Each model is available as suction feed or pressurized feed and suction feed pumps can be fitted with a sight glass for visually verifying operation. All pumps are now equipped with a roller bearing on the rocker arm. The roller bearing keeps the rocker arm from cutting a groove in the lube box cam and ensures that the proper amount of lubricant is delivered over the long run. Without the roller bearing, the wear on the cam will reduce the displacement of the rocker arm and will continually reduce the amount of lubricant fed to the system.
· One piece steel pump body
· Precision roller rocker assembly
· Pyrex sight glass with protective housing
· Precision internal and outlet check valves
· Weatherproof construction
· Furnished as original equipment by engine, pump and compressor manufacturers
· 3 pump types: vacuum, gravity, pressure
· 3 pump sizes: 3/16”, 1/4”, 3/8”
· Modular cylinder design
CPI2012E Pump
The CPI2012E Pump is designed primarily but not exclusively for the European pump market, the 2012E Pump has been produced with proven pump configurations. Features include heavy duty casting, double ball discharge connector, modular cylinder and suction tube with strainer. Available in box suction, gravity fed and pressure fed models.

Model P-55U
The Model P-55U Pump is an up-grade of the Premier Model P-55. The patented one piece steel pump body with modular cylinder assembly represents the latest in pump design. The Model P-55U Pump is designed to fit in Premier, Mega, McCord and Lincoln reservoirs.
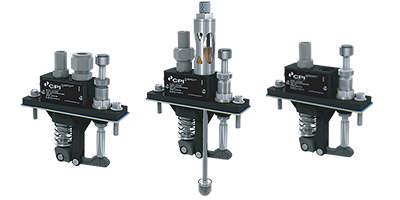
Model 2000 Pumps
Note: Model 55 now replaces all Model 2000 pumps. Model 2000 pumps were a direct replacement pump assemblies for use in: Manzel Model 76 and 88 Lubricators.
Model 2001 Pumps
Are designed to replace Manzel Model 94V and 100V Lubricators.
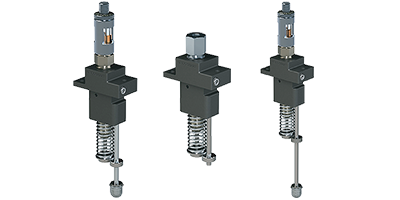
Model P92
Replacements for Madison Kipp style pumps: Models DSL, SVH and SVK.
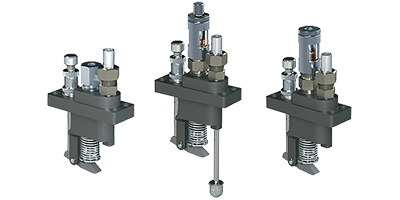
· Ariel
· Trabon
· Graco
· Lubriquip
· Manzel
· Ajax
· Lincoln
· Premier
· Progressive
· Chicago Pneumatic
· Energy Industries
· Ingersoll Rand
· Cooper Axis
· Dresser-Rand
· Gemini
· White Superior
· Worthington Cub
· Cooper Bessemer
· Clark
· Coulthard
* All trademark names are the property of their respective companies and not associated with CPI.
Bulletin: Lubrication Product Guide
(LUBEPROD.1803.LTR)
Sales Overview: Lubrication Systems
(LS.1506.LTR)
Sales Bulletin: Model 2012E Lubricator Pumps
(P2012.1702.LTR)
Sales Bulletin: Model P55 Lubricator Pumps
(P55.1702.LTR)
Installation & Operations Manual: Model P55 Lubricator Pumps
(65015000094573_B)
Sales Bulletin: Model 2001 Lubricator Pumps
(P2001.1702.LTR)
Sales Bulletin: Model P92 Lubricator Pumps
(P92.1702.LTR)
CPI manufactures hundreds of different sizes, ratios and mounting configurations designed to fit your old or new engine, pump or compressor.
CPI manufactures hundreds of different sizes, ratios and mounting configurations designed to fit your old or new engine, pump or compressor.
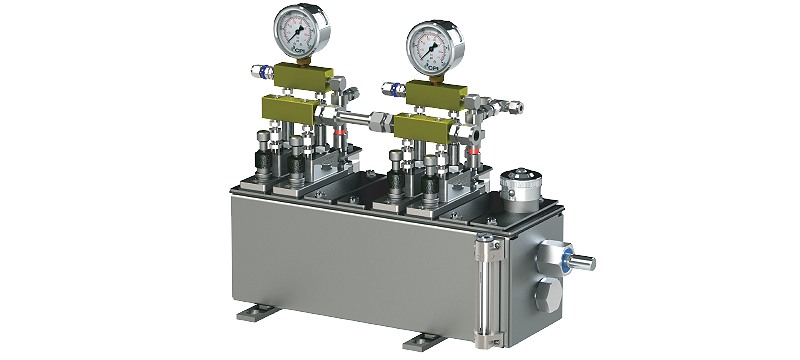
CPI Lubricators will accurately deliver a predetermined quantity of oil normally under pressure, at regular intervals to moving parts on all types of industrial machinery. The lubricator consists of a reservoir, drive mechanism, and oil pumps. They are furnished in electric motor drive or shaft driven from the machinery to be lubricated. Shaft driven units can be direct drive, pulley/sheave, or oscillating drive motion.
Applications may include engines, pumps, compressors, natural gas compressors, machine tools, printing presses, steel mills, pulp & paper mills, spindles, textile machinery, tap/die lubrication, lumber mills, transfer presses, mobile equipment, mining, and woodworking.
· Force feed lubricators
· Heavy duty steel reservoirs
· All gear rotary drives
· Electric motor drives
· Ratchet drives
· Bottom rotary drives
· Suitable for use with petroleum and synthetic based lubricants
· Automatic oil level controllers
· Level switches
· Electric heater and thermostat assemblies
· Shaft rotation alarms
· Partitions in reservoir for two or more lubricants
· Check valves available in carbon steel and stainless steel
· Ariel
· Trabon
· Graco
· Lubriquip
· Manzel
· Ajax
· Lincoln
· Premier
· Progressive
· Chicago Pneumatic
· Energy Industries
· Ingersoll Rand
· Cooper Axis
· Dresser-Rand
· Gemini
· White Superior
· Worthington Cub
· Cooper Bessemer
· Clark
· Coulthard
* All trademark names are the property of their respective companies and not associated with CPI.
Divider blocks (also known as distribution blocks or divider valves) provided by CPI, precisely allow correct lubrication rates to be distributed to up to six points, reducing the size of lubricator boxes and allowing proper lubrication. CPI provides high quality accessories and patented products that allow constant monitoring and simplify troubleshooting. They are available in three mounting configurations to match the mounting arrangements of Dropsa, Trabon and Lincoln.
ADVANTAGES OF DIVIDER BLOCKS / DIVIDER VALVES
The single line progressive hydraulic circuit divider block, requires only one piston to be monitored to assure proper operation of the entire lubrication system - one moves they all move.
Lubricator reservoir is smaller to accommodate fewer pumps - most systems designed to use one pump.
Output monitored at the divider block is a true measurement of the quantity of lubricant delivered to the compressor. Extremely precise amounts delivered to each injection point.
They are very simple to use and maintain:
· Less parts/shorter tubing runs
· Simplified trouble shooting with accessories
· Fewer pumps are responsible for the pressure and output of every lube point
Divider blocks (also known as distribution blocks or divider valves) provided by CPI precisely distribute correct lubrication, reducing the size of lubricator boxes and maximizing lubrication system efficiency.
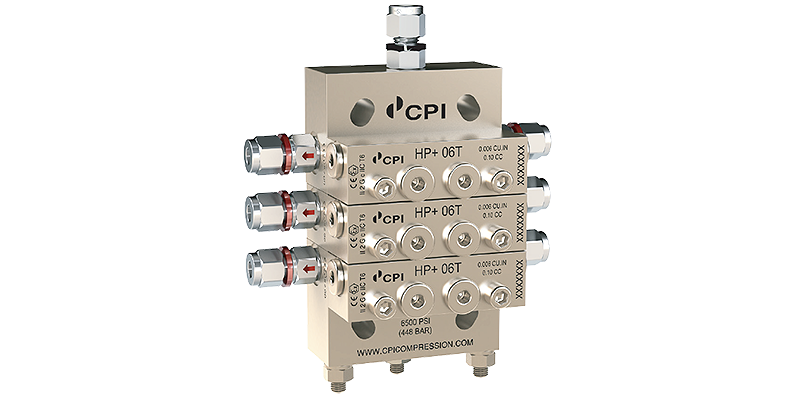
CPI’s HP+ Divider Blocks are a High Performance product line featuring:
· Standard base plate assembly mounts to multiple traditional industry bolt patterns.
· Simplified ordering process to save time and reduce errors.
· Improved performance for applications up to 6500 PSI (448 BAR).
· Improved piston to bore geometry for consistent oil output and longer product life.
· Improved overall sealing with precision CPI Custom 1/8 ORB (O-Ring Boss) port geometry.
· Complete assembly standard with O-ring seals eliminating leakage and need for sealant.
· Each assembly comes standard with Custom ORB inlet tube fitting.
· Improved corrosion resistance with all components nickel plated.
· All base plate assemblies feature internal check valves for added performance protection.
· Standard O-ring seals are VITON® O-Rings (FKM) for improved chemical and heat resistance.
· Each divider block assembly is easily configured to the customer’s specific lubrication needs.
Sales Bulletin: HP+ Divider Blocks
(HP+DB.1608.LTR)
User Instructions: Divider Blocks
(650150000093927_A)
When you can't afford compressor down time!
Divider blocks (also known as distribution blocks or divider valves) provided by CPI precisely distribute correct lubrication, reducing the size of lubricator boxes and maximizing lubrication system efficiency.
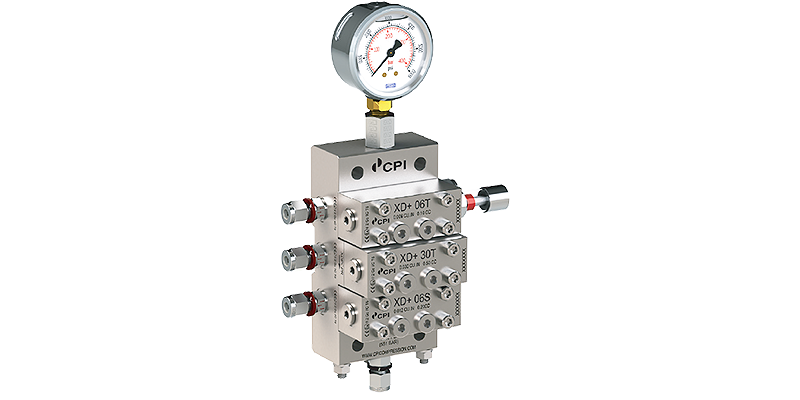
CPI’s XD+ Divider Blocks are an Extreme Duty Performance product line featuring:
· Symmetric element design adds mass around the piston for improved performance at higher pressures by reducing piston bore warping and expansion.
· Improved piston to bore geometry for consistent oil output and longer product life.
· Extreme performance for applications up to 8000 PSI (551 BAR).
· Simplified ordering process to save time and reduce errors.
· Improved overall sealing with precision CPI Custom 1/8 ORB (O-Ring Boss) port geometry.
· Dual inlet ports on top and bottom of divider block assembly for added flexibility.
· Complete assembly standard with O-ring seals eliminating leakage and need for sealant.
· Each assembly comes standard with Custom ORB inlet tube fitting and ¼” NPT adapter fitting.
· Improved corrosion resistance with all components nickel plated.
· All base plate assemblies feature internal check valves for added performance protection.
· Standard O-ring seals are VITON O-Rings (FKM) for improved chemical and heat resistance.
· Each divider block assembly is easily configured to the customer’s specific lubrication needs.
Sales Bulletin: XD+ Divider Blocks
(XD+DB.1608.LTR)
User Instructions: Divider Blocks
(650150000093927_A)
Divider blocks (also known as distribution blocks or divider valves) provided by CPI precisely distribute correct lubrication, reducing the size of lubricator boxes and maximizing lubrication system efficiency.
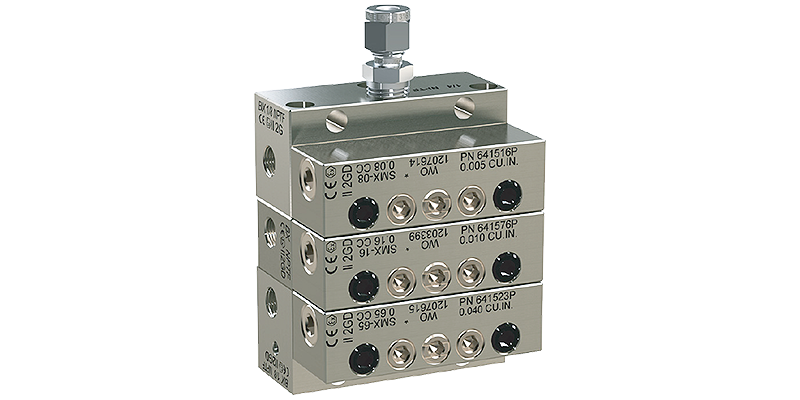
CPI offers the DropsA SMX product line as an affordable performance product featuring:
· Multiple base plate assembly mounting patterns for traditional industry bolt patterns.
· Simplified ordering process to save time and reduce errors.
· Proven performance for applications up to 4000 PSI (276 BAR).
· Base assemblies are bolted together with a threaded insert and attachment screw. This provides no maximum limitation on the number of elements which can be used on the assembly.
· A bypass element is available to accommodate an increase or decrease in lubrication points without disturbing the base assembly or pipe work. This element acts as a blank placeholder and is only used on four section or larger divider block assemblies.
· Each divider block assembly is easily configured to the customer’s specific lubrication needs.
Sales Bulletin: SMX Divider Blocks
(HP+DB.1608.LTR)
User Instructions: Divider Blocks
(SMXDB.1608.LTR)
NEOMAG Visual Cycle Center
The CPI patented NEOMAG visual cycle indicator follows the divider block piston movement so the operator can monitor and control oil consumption, set lube rates and easily spot problems in the divider block system.
Features of NEOMAG :
· No oil reduction
· Reflective orange cycle indicator visible for over 30 feet
· Shows actual movement of divider block
· O-ring seal eliminates leakage to 10,000 PSI
Base Plate Outlet Check Valve
Base Plate Check Valves help keep divider blocks free from air by sealing the flow of lubrication in the positive direction. This keeps the divider block filled with lubricant and ready to go on systems even if they are repeatedly started and stopped.
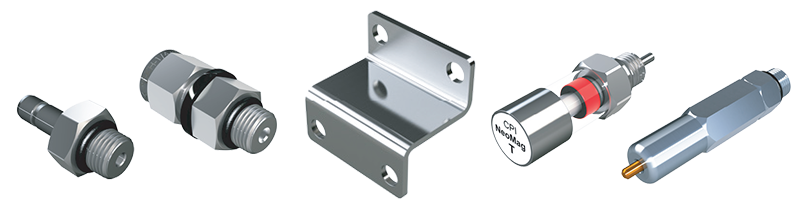
The base plate outlet check valve from CPI assures reliable operation of the divider block system. The O-Ring seal design on the base plate outlet sections ensures exceptional sealing and ease of assembly. The O-Ring seal, base plate check valves, with integral tube connections are manufactured and available only through CPI.
Reset Pin Indicator
Many man hours are wasted needlessly when an operator has to find a compressor or packing lubrication point that is causing high pressure in the divider block system. The operator must loosen every lubrication line and check each point one at a time with a purge gun to find the plugged point.
Spring Loaded Pressure Indicators are pressure sensing devices that enable the operator to immediately locate the injection point causing the excessive pressure or the location of a blocked tubing line in the divider.
Capture Proximity Switch
Compressor Product International's proximity switch sends a switch closure with each cycle of the divider block to the control panel, PLC or the Proflo PF1, to monitor oil consumption and shutdown the compressor if the lubrication system begins to deteriorate.
Sales Bulletin: Divider Blocks Accessories
(DBA.1805.LTR)
CPI offers a range of high quality check valves to be used on compressors and divider block systems including extreme duty check valves with check valve protectors and double ball check valves.
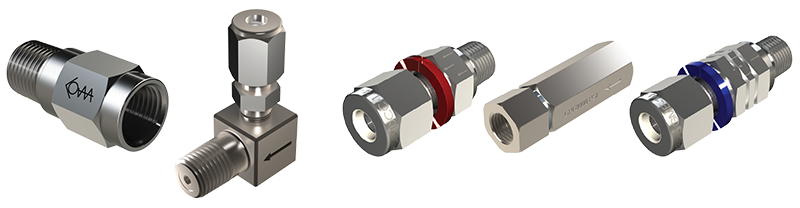
The XDC from CPI is a modern redesign of the traditional check valve. Instead of the old fashioned 'ball' design, the XDC uses a self guiding, double poppet with Viton O-Rings. That along with the stainless steel design makes the XDC the most reliable check valve available today. Additionally, the integral tube connector reduces potential leak paths and makes installation a snap.
Features:
· Lightweight reduces failure caused by vibration
· Self guiding poppets ensure positive sealing
· 8,000 PSI - 400°F
· Integral tube connector eliminates leak path
CVP Check Valve Protector
The CPI CVP check valve protector installed with the CPI XDC extreme duty check valve is designed to eliminate check valve failure caused by heat & gas stream contamination.
Size matters. Unlike traditional check valve protectors, this assembly allows minimum oil capacity, reducing the amount of time at startup before oil actually gets to the injection point. The minimal design also eliminates fatigue failures from vibration typical of the older and larger check valve protector designs.
Features:
· Provides oil barrier to protect the check valve sealing surfaces from hot gas and trash in the gas stream
· Minimum fill capacity allows immediate delivery of oil to cylinders and packing
· Pressure gauge port enables the operator to visually see when the rod packing is failing
Omni Trap Failures?
A common cause of Omni Trap failure is the weight of the product and vibration of the compressor. The total weight of the "CVP-XDC" combination check valve and oil head fitting is 4oz. The lightness of this product reduces the possibility of failure caused by vibration. Fill capacity of .010 will require less than two (2) cycles of a number 6 (.006) piston to begin lubricating at the injection point. With an operating pressure of 10,000 PSI and 400°F, this combination addresses the need for check valve reliability, protection of compressor components and operator safety.
CPI Double Ball Check Valves are designed for high pressure applications where reverse flow / leakage must be kept to minimum. Typical applications include engine, pump and compressor cylinder / packing lubrication and hydraulic systems. A relatively stiff spring in these check valves serves to increase the reliable of the circuit.
Operation:
Flow entering the check valve creates pressure on the smaller ball (5). If the pressure created is higher than the opposing force of the spring (3), the smaller ball is moved off its seat. This allows flow to create a similar pressure and action on the large ball (6) and spring (4). Flow continues on to the outlet of the check valve. If flow is reversed, flow force and spring (4) cause the large ball (6) to be reseated. Any leakage around the large ball (6) is blocked by the smaller ball (5) that is firmly seated by spring (3).
Sales Bulletin: Check Valves
(CHECKVALVE.1704.LTR)
No flow devices detect lubrication system failures and shut down the compressor before costly damage can occur to the compressor. Operating without meaningful system data, using inferior parts or relying on outdated technology is a high risk, low reward catastrophe waiting to happen.
CPI offers a wide range of reliable no flow devices including the state of the art Proflo PF1 which not only monitors system operation, it stores the system data for retrieval, analysis, and predictive maintenance. The mid range Proflo Jr. is a direct replacement for DNFT's. It is designed for a long and trouble free life operating in even the harshest conditions. At the entry level, CPI offers the capture proximity switch that provides basic no flow detection functionality and easily ties in with existing divider blocks and system control panels. CPI also stocks mechanical no-flow devices.
Divider Block Monitor and No-Flow Shutdown Protection
Overview
The Proflo PF1 monitors operation of the divider block system by detecting each cycle of the system. If the pump fails or the cycle time of the divider block system slows down or speeds up the Proflo monitor alerts the operator by displaying the changed cycle time on the LCD display. If the pump deteriorates the cycle time will slow down and the Proflo will change to alarm state and shutdown the compressor, preventing damage to the compressor cylinders, pistons, rods and packing.
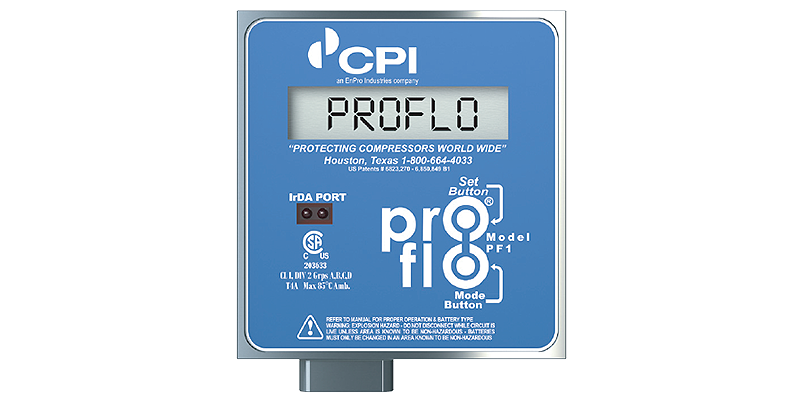
Description
The Proflo monitor is 21st Century engineering, utilizing state-of-the-art communication technology and data storage. The unit protects the compressor and end user by monitoring movement of the divider block piston and detecting slow flow and no flow of the fluid flow system. The control housing can be mounted in a control panel or directly to any compressor divider block “Trabon, Lubriquip, SB, Lincoln, Dropsa”.
The PF1 operates on field replaceable “AA” Alkaline batteries with expected life of up to 2 years. The LCD indicates when the batteries should be changed. If battery voltage drops below safe operating levels the Proflo monitor will go into alarm mode and warn the operator of battery failure. Bi-polar wiring allows for simple trouble free wiring to the control panel.
The unit incorporates a liquid crystal display to indicate the following: A. Operating time of the compressor. B. “Average”, “Last” and “Current” cycle time of the divider block. C. Total divider block cycles. D. Battery power status. E. Alarm set time for no flow warning. F. Alarm wiring mode: Normally Open/Normally Closed.
The cycle time display enables the operator to easily set and monitor pump rates. All trending data and set points are stored in Electrical Erasable Programmable Read Only Memory, (EEPROM). Memory is not lost due to battery failure or change.
The PF1 capitalizes on proven technology and components to monitor fluid consumption every 30 minutes, run time of the compressor and trends the operation of the divider block system and oil consumption for 365 days. This device will give the compressor operator a superior product with features never before possible in the industry.
Features:
· Trends and stores divider block system operation to monitor and prove:
· oil consumption - over and under lubrication
· lubricator pump failure
· divider block failure
· compressor component failure - rings, rod, packing and cylinders
· compressor run time
· Shuts down compressor when lubrication system fails or begins to deteriorate
· Adjustable alarm time
· Installs on divider block or in control panel
· Wireless (IRDA) download of trending information to any hand held Palm Pilot or Palm cell phone device
· Automatically uploads all files to computer and converts information to Excel
Sales Bulletin: ProFlo PF1 & PF1 24V Shutdown Devices
(PPF1.1801.LTR)
Wiring Diagram: Proflo 24 VDC Power
The Proflo USB-IR Adaptor and Proflo Assist Software have been designed to work with our Proflo PF1 monitoring device to allow the user to translate data collected from the PF1 to adjustments needed on the existing lubrication pumps, assisting in reducing over or under-lubrication.
The Proflo USB-IR adaptor allows the direct transfer of information from the PF1 device to the user’s computer.
The PF1 monitoring device records the average cycle time for each 30 minute block of operation and can transmit this information via infrared signals. Then the Proflo USB-IR adaptor captures the IR signals that are broadcasted by the PF1 device, and, through the use of the software, translates those signals into information that the user can use to regulate their lubricator pumps.
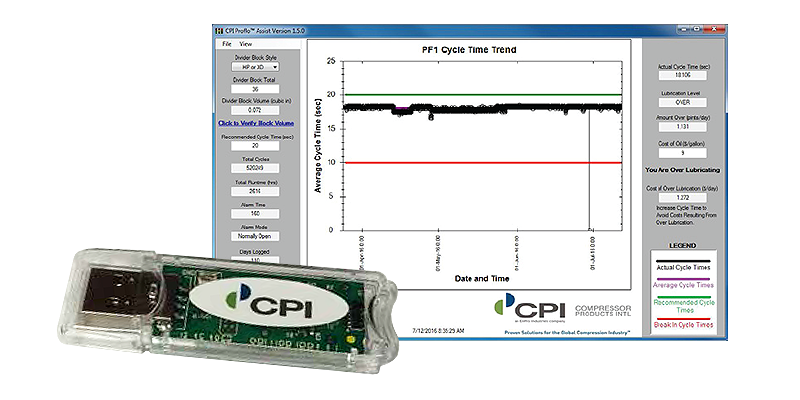
Features:
· User friendly software
· Small and portable USB
· Immediate data collection
· Can retrieve information that has been stored on the PF1 device for months
· One Adaptor can be used on all of the user’s PF1 devices
· Recommended pump adjustment
· Save data in Excel format
· Easy to view trend graph
· Cost savings analysis
Sales Bulletin: ProFlo USB-IR Adaptor and ProFlo Assist Software
(PA&PAS.1608.LTR)
Reliable No-Flow Shutdown Protection
Overview
The Proflo Jr. monitors the operation of the divider block system by detecting each cycle of the system. If the pump deteriorates or if the lubricant flow slows down the cycle time of the lube system will fall below the specified alarm time and the Proflo Jr. will change to alarm state and shutdown the compressor preventing damage to the compressor cylinders, pistons, rods and packing.
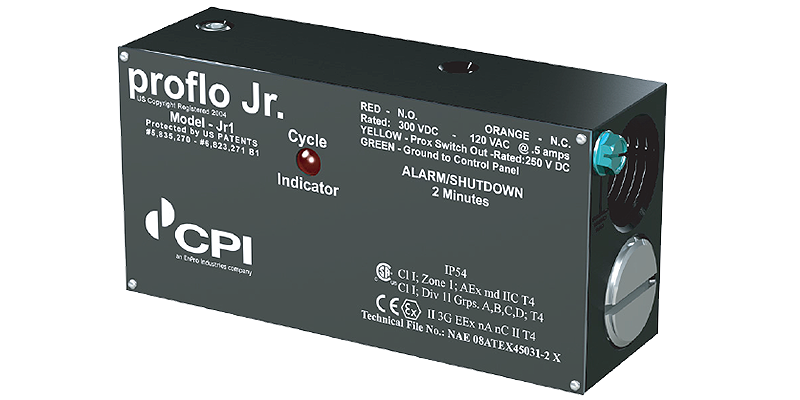
Description
The Proflo Jr. is a totally enclosed electronic device, combining the latest technology in microprocessor and transistor components for detecting Slow-Flow and No-Flow of divider block lubrication systems. The Proflo Jr. incorporates an oscillating crystal to accurately monitor the cycle time of the lubrication system to enable precision timed shutdown capability. The magnet assembly and electronics are designed to withstand extreme vibration for compressor applications.
The Proflo Jr. operates on a 3.3 Volt hermetically sealed high temp Lithium battery, with expected life of 10 years. If battery voltage drops below normal operating levels the Proflo® Jr. changes to alarm state and the compressor cannot be restarted. The LED flashes with each divider block cycle to enable the operator to easily set and monitor lubrication rates as recommended by the compressor manufacturer.
Operation
Lubricant flow through the divider valve assembly forces the pistons to cycle back and forth causing a lateral movement of the magnet linked to the piston. Movement is monitored by the microprocessor which resets the timer, lights the LED, and allows the unit to continue operation. The flashing LED indicates one complete cycle of the lubrication system. The microprocessor must receive this cycle in a predetermined time or a shutdown will occur.
Features:
· 3.3 volt hermetically sealed high temperature battery
· AC or DC operation, switch rated for 300 VDC and 120 VAC @.5 amps
· Patented sealed magnet assembly, No lost magnets, springs or spacers EVER
· Heavy duty magnet housing eliminated possibility of failure caused by bending
· Proximity switch output is standard with every unit
· Hall effect activated
Sales Bulletin: Proflo Jr. Shut Down Devices
(PJR.1701.LTR)
Installation Bulletin: Proflo Jr.
Over time lubrication pumps will wear and slowly decrease output throughout their lifespan on a compressor. The Proflo EOS will automatically account for pump wear, and once the output starts to decrease, the EOS will adjust to increase the flow to maintain the desired set-point. By providing optimal timed stroke adjustments the Proflo EOS will support lubrication oil savings immediately after install on your compressor.
The Proflo EOS constantly monitors the quantity of oil cycling through the divider block via the signal from a no-flow shutdown device. When the quantity of oil delivered to the compressor unexpectedly changes the Proflo EOS compensates for this, always ensuring an optimum lubrication level.
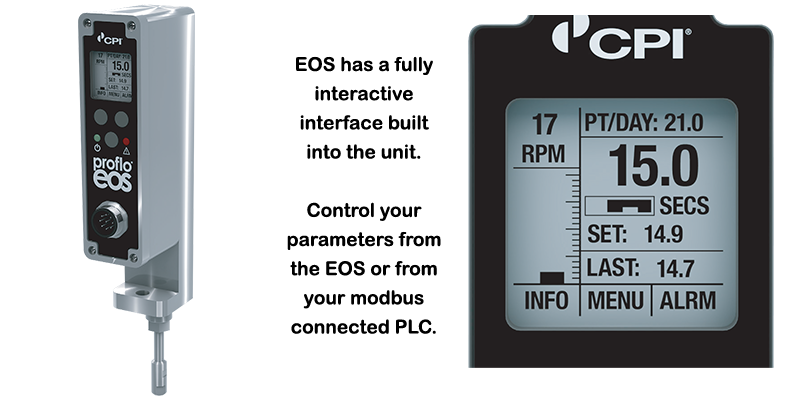
Features:
· Replaces the traditional pump manual adjuster
· Receives feedback from Proflo PF1, Proflo Jr or proximity switch
· Ensures optimum compressor lubrication
· Maintains optimum hydraulic locking of packing rings
· Increases performance of piston rings
· Reduces valve "sticktion" and carbonizing of elements
· Decreases emissions and carbon footprint
· Reduces downstream pipeline scrubber replacements
Sales Bulletin: Proflo EOS
(PEOS.ENG.1809.LTR)
Are you having premature failure of cylinders, rings or rod packing?
The compressor industries' “only” lubrication monitor capable of monitoring a single lubrication point to determine the exact quantity of oil injected into the cylinder or packing with the compressor running at normal operating temperatures and pressures (US Patent 6,823,270 - 6,850,849).
Tests the reliability of the divider block and lube pump to determine possible cause of premature failure of cylinders, rings and rod packing.
The CPI lubrication group offers the highest quality compressor lubrication systems available in the industry today. Our experience, commitment to excellence and innovative products, has earned us the reputation as an industry leader for introducing the latest technology and expertise in compressor lubrication.
Our Engineers and Technicians make it their responsibility to work closely with customers to ensure that the lubrication systems we provide are designed, assembled, tested and shipped to meet each customers specifications.
The CPI offers the highest quality compressor lubrication systems available in the industry today. Our experience, commitment to excellence and innovative products, has earned us the reputation as an industry leader for introducing the latest technology and expertise in compressor lubrication.
Our Engineers and Technicians make it their responsibility to work closely with customers to ensure that the lubrication systems we provide are designed, assembled, tested and shipped to meet each customers specifications.
CPI designs divider block systems for all compressors in the industry, utilizing our extensive field and design application experience. Systems are designed to reflect operating temperatures, pressures and gas stream components.
The CPI SAFEGUARD 5000 Lubrication System Console has been designed as a standalone lubrication console for hazardous locations and all types of industrial machinery including reciprocating compressors and reciprocating pumps.
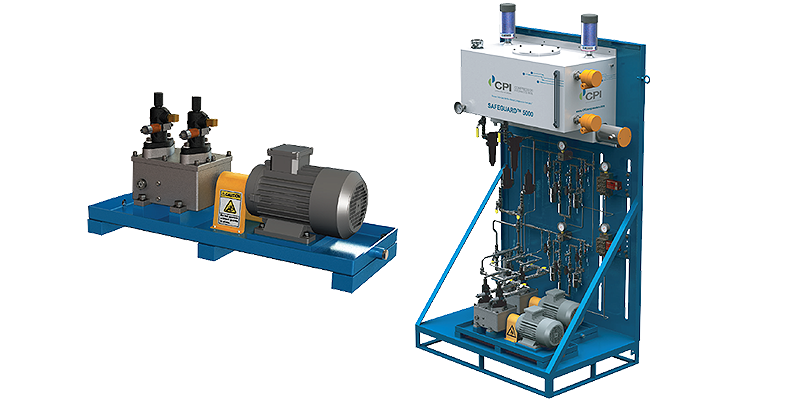
The SAFEGUARD 5000 lubrication system console is designed to work with CPI’s extensive line of divider blocks and Lubrication System Accessories to provide precise lubrication to your machinery.
Sales Bulletin: Safeguard 5000 Lubrication System Console
(SG.1506.LTR)
As an integral part of our business, CPI carries a complete variety of innovative, high quality, reliable lubricators, pumps and accessories for engine and compressor applications, including:
· Divider Blocks
· Cycle Indicators
· Proximity Switches
· Check Valves
· Pressure Indicators
· Lube Oil Monitors
· Pumps
· No-Flow Shutdown Devices
High Pressure In-Line Filter
Provides maximum protection for system components.
Low Pressure Filter
The Delta-P Filter adapter filters lubricant through a 25 micron filter on the low pressure feed prior to the suction manifold on the high pressure pump assemblies. Filtering the lubricant prior to the pumps will keep debris from damaging the high pressure system components. The dual gauges provide an easy way for the operator to determine when to change the filter, based on rising differential pressure.
High Pressure In-Line Stainless Steel Filter
The new S.S. filter housing is not affected by harsh environments (offshore salt environment or high concentrations of H2S gas) like the Aluminum filter housing, so it can be used for all compressor divider block system applications and all applications for our new chemical injection divider block systems.
The new S.S. element comes in 10 and 25 micron.
ENVIRONMENT: Element is not affected by H2S as the old bronze element. Even if the crankcase has oil saturated by H2S, this new element and housing will continue to filter the oil and keep the compressor operating at peak efficiency. The old sintered bronze element deteriorated when it was exposed to H2S and plugged completely causing the compressor to shut down from lube no flow.
FILTER AREA: The new S.S. pleated element has over 6 times the filtering area compared to the old sintered bronze element in all competitors filters which means we have extended the life of the element and reliability of the compressor. Now we will recommend changing the filter element every 2 years in place of one year.
WASHABLE FILTER ELEMENT: Although we do not recommend washing any filter element, if the end users compressor goes down due to a plugged filter element, this new S.S. pleated element can be washed with a air gun and cleaning fluid and replaced in the housing to keep the compressor running until a new element can be ordered and installed.
The CPI purge gun provides a convenient, cost effective method to remove all air from the divider block system to ensure all lubrication points will receive lubrication immediately on start-up of the compressor. The manual pump is also an efficient device to trouble shoot the divider block system to locate blockage in divider blocks, tubing lines, and cylinder/packing injection points.
The pump delivers full pressure at minimum stroke for ease of use in tight quarters. All pumps are provided with a 36” stainless steel braided hose for long reach applications, 5000 PSI stainless steel liquid filled pressure gauge and chrome plated steel tube with bulls eye sight glass.
Features:
· Heavy duty cast aluminum alloy pump head
· Precision fit, hardened plunger develops 5,000# pressure
· Chrome plated steel reservoir
· Visual level indication eliminates injecting air into the divider block system
· Stainless steel liquid filled pressure gauge
· 36” stainless steel braided hose with all tubing connection
Never replace a rupture disk again!
The divider block system is protected from overpressure conditions by the Pop Open Pressure Relief device, or ‘POPR’. This innovative device, only available from CPI, replaces the old style and unreliable rupture discs. When the divider block system over pressures, the "POPR" snaps open and diverts the oil to the lubricator reservoir, a closed container, lube pump oil supply line or back to the compressor frame. Unit "always" remains in open position until reset by the compressor operator. Once the system blockage has been fixed, simply reset by closing the POPR.
Guaranteed to work with all CCT, Ariel, Trabon, Lubriquip, SB, GRACO, Manzel, Lincoln & Dropsa divider block systems.
Remove the Atmospheric Rupture Assembly & Install the “POPR”.... It’s that easy!
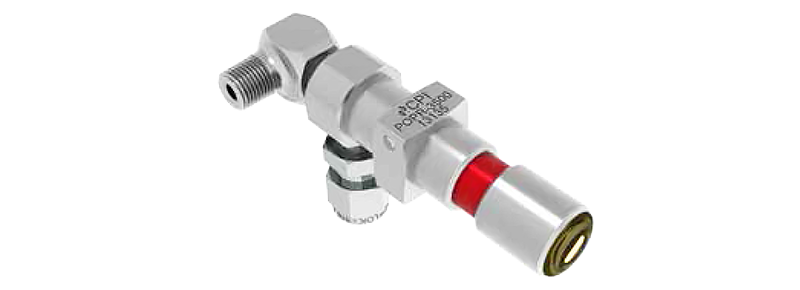
Features of the POPR:
ENVIRONMENT: Eliminates Oil Spills Caused by Blown Rupture Disc
SAFETY: Protects Operator from Possible Injury by High Pressure Oil Squirting from Blown Rupture Disc
RELIABLE: Opens at Specific Set Pressure to Protect Compressor from Damage
PROTECTION: Remains in Open Position Until Reset by Operator With a Simple Push on the Top of the Assembly
Sales Bulletin: POPR - Pop Open Pressure Relief Valve
(POPR.1603.LTR)
Features:
· Eliminates premature wear of divider blocks
· Reduces piston by-passing
· Eliminates blown rupture disc problems
· Simplifies balancing the divider block system
The divider block system operates efficiently, only when pressure differentials between injection points in the system do not exceed 1000 PSI. If the system is not balanced properly, the pressure can cause the pistons to wear prematurely and allow the oil intended for the high pressure injection point to flow around the worn piston to the point with least resistance (lower pressure). By-passing oil will cause serious damage or premature failure to the compressor cylinders, pistons, rings, rod and packing gland.