CPI Wear Products
CPI designs and manufactures a wide range of high quality sealing and wear components, custom sized according to the needs of the compressor. Unmatched technical knowledge allows CPI to select the ideal material for any application, including metallic, non-metallic or one of many special polymer alloys.
CPI materials for pump wear parts are proprietary polymer alloys designed for pump bushing wear rings, guide bushings and thrust washers in liquid pumps. The CPI materials are intended to reduce diametral clearance on pump wear parts without the risk of damage to metal components. The properties of these materials are designed to help avoid catastrophic pump failures caused by dry-run start up or excessive vibration.
CPI combines a wide variety of materials and designs to meet any specific packing ring or oil wiper ring requirement - Cast iron, and bronze are just a few of the materials available. All of these materials are available in packing rings and oil wipers designed for unidirectional and bi-directional sealing, low pressure vent sealing, and gas purge sealing.
CONTINUING A TRADITION OF QUALITY STILL USED TODAY
CPI offers a variety of packing and wiper rings to satisfy operator's requirements in selected materials specific to their application. Packing rings are the elements which make the seal, compensate for wear, movement of the rod, and temperature change. There have been many patents obtained on various types of packing rings; however, the most popular and widely used design is that patented by A. W. France, November 7, 1899.
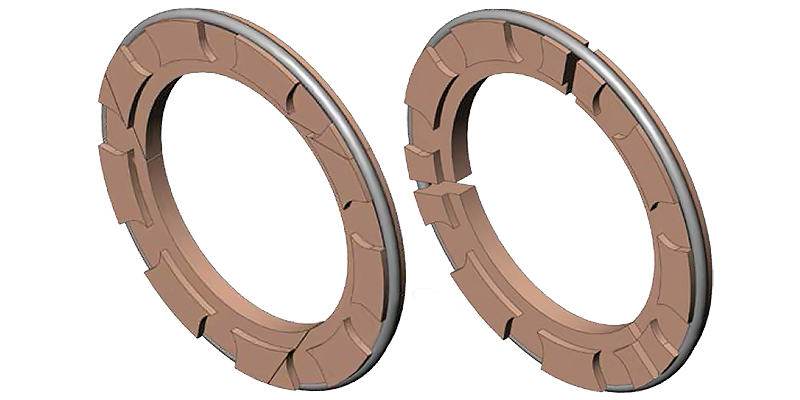
CPI combines a wide range of metallic and non-metallic materials and a variety of designs to meet with many typical packing requirements and also the more specific and problematic ones.
The range of materials that CPI utilizes are available across the broad range of packing rings designed for unidirectional and bidirectional sealing, low pressure vent and gas purge sealing. This also includes high-speed and high pressure rings, as well as sandwich and triple circle designs.
Basic Packing Ring Designs:
· Single acting seal rings/pairs
· Double acting seal rings/pairs
· Backup rings
· Pressure breakers
· Pressure breaker with relief slots
CPI oil wiper rings are designed to effectively provide positive containment of lubricants within the crankcase. The CPI scraper is designed specifically for those applications where total oil control is necessary. Most reciprocating compressors use oil control or wiper rings to prevent crankcase oil from passing into the cylinder and in some instances to prevent condensate and cylinder and packing lubricant from entering the crankcase.
Segmented wiper rings may be either radially or tangentially cut. They are garter spring actuated. The scraper edges in contact with the piston rod are proportioned to give a bearing load sufficient to break the surface tension of the oil film on the rod and wipe it away. While there are many variations and innovations of wipers, there are basically two types. Normally two or three wipers are used in an oil seal and as previously indicated may be used as a part of or in conjunction with a pressure packing.
The CPI scraper is designed specifically for those applications where total oil control is necessary. Available in both cast iron and bronze, the unique design and operation of these rings provide extremely effective containment of lubricants in their intended area as well as long trouble free service.
The unique design and operation of these rings provides extremely effective containment of lubricants and long trouble-free service.
Basic Wiper Ring Designs:
· Tangent cut unidirectional
· Tangent cut bidirectional
· Radial cut wiper rings
· CPI Special Polymer Alloys
· PTFE
· Thermoplastics
· Bronze
· Cast iron
Installation Bulletin: Packing Rings
(PACKRINGS.1506.LTR)
Sales Bulletin: Oil Wiper Rings
(WIPERRING.1708.LTR)
CPI designs and manufactures a full line of compressor packing cases, intermediate partition packing cases and wiper cases for your reciprocating compressor’s piston rod sealing system. Precision machined from cast iron, bronze alloy steel or stainless steel.
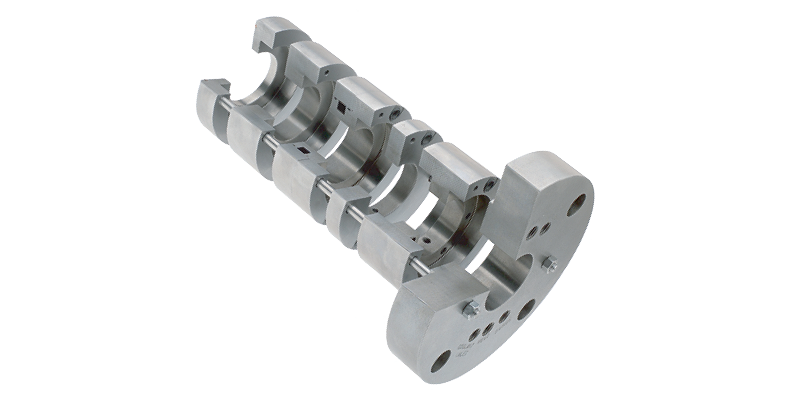
TO SATISFY OPERATING REQUIREMENTS
CPI designs and manufactures a full line of compressor packing cases, intermediate partition packing cases and wiper cases for your reciprocating compressor’s piston rod sealing system.
· Precision machined from cast iron, bronze alloy steel or stainless steel
· All packing and wiper cases are designed to be easily reconditioned when needed to maximize service life
· Available in cooled or non-cooled for use in both oil-free and lubricated applications to satisfy the full spectrum of temperatures, pressures and corrosive conditions
· Designed to meet all environmental concerns and regulations including available vent and purge designed assemblies for fugitive emissions reductions
The packing case assembly is critical to the proper operation of the piston rod packing and the sealing of the cylinder. The CPI packing case has several important features that help to maximize your compressor’s performance:
· Cylinder-end gasket to prevent process gas from bypassing the packing rings
· Precision-machined mating and sealing surfaces to prevent leakage
· Provides passages for lubrication, vent, coolant and buffer gas as required
· Flange with adequate bolting to maintain gasket seating and seal between cups at operating pressure
· Recess in each cup to contain free floating seal rings
With the ever increasing concern for the effects upon the global environment, systems to control emissions are becoming even more important. As part of its commitment to its customers and the environment, CPI has a range of purge control systems that maintain buffer pressure and monitor gas flow and packing condition to eliminate emissions from packing cases used in reciprocating compressors. The purge-gas system prevents your process gas from escaping through the packing case by introducing an inert buffer gas into the assembly.
CPI can convert your existing case to a purge design. Converting your packing case to a purge-gas system allows you to monitor your packing ring life and comply with tough emissions regulations. Our standard purge design employs a two groove T-cup. If the length of the assembly is limited, a single groove cup arrangement is used.
Sales Bulletin: Packing Cases
(PC.1701.LTR)
Sales Bulletin: Mechanical Packing Design/Theory
(MECHANICALPACKING.1506.LTR)
A range of piston rings, rider rings and rider bands fulfill the varied sealing and piston support requirements for reciprocating compressors, using a range of CPI Special Polymer Alloys, standard and special materials.
Many successful field applications, using the unique range of CPI materials, have transformed both oil-free and lubricated compressor reliability, resulting in better sealing, less wear and longer running life.
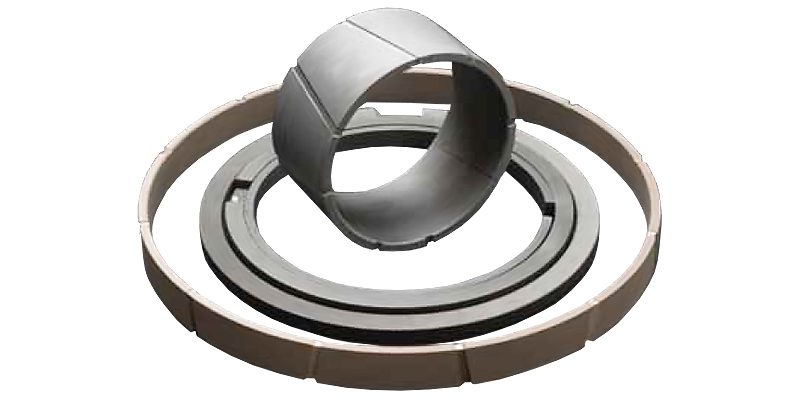
TO SATISFY OPERATING REQUIREMENTS
Application-engineered piston and rider rings are available, specifically designed to meet your operating parameters. On-site blending and compression or injection molding enables CPI to maintain total control throughout the manufacturing process.
· Provide excellent sealing capabilities
· Piston support
· Available in a variety of designs and materials to best suit your application requirements
A range of piston rings, rider rings and rider bands fulfill the varied sealing and piston support requirements for reciprocating compressors, using a range of CPI Special Polymer Alloys, standard and special materials. Many successful field applications, using the unique range of CPI materials, have transformed both oil-free and lubricated compressor reliability, resulting in better sealing, less wear and longer running life.
CPI’s commitment to the manufacture of quality components is vitally important. Each facility adheres to meticulous and stringent procedures to maintain quality assurance to ISO 9001 standards.
The CPI manufacturing process benefits from total control and traceability of materials, within-house blending and moulding facilities through to the manufacturing and distribution of our precision engineered and quality components. All CPI’s manufacturing facilities are equipped with cutting edge production technologies of precision, automated and CNC machinery, operated by a highly skilled, experienced and dedicated work force.
· One-piece or segmental straight
· Angle cut
· Step cut
· Twin Ring
· Double Twin Ring
· Two Segment
· Pressure balanced
CPI also custom designs rings and has developed specific combinations for particularly problematic and demanding applications. This has also included numerous successful conversions from lubricated to non-lubricated operation. Pressure balanced rings are available, when deemed appropriate for high pressure applications and piston/rider ring combinations are also available for more specific applications.
Large diameter piston rings up to 47” (1200mm) are custom manufactured for special requirements. A range of metallic piston and rider rings are also manufactured, using selected grades of bronze or cast iron, where operational requirements dictate.
Sales Bulletin: Piston and Rider Rings
(PISTONRIDER.1506.LTR)
CPI’s Emissionguard TR2 packing ring is the only ring design that multiplies the benefits of a tangent to rod ring and a step tangent ring by combining the two rings into one, providing a more efficient seal, reduced friction and extended lifetime.
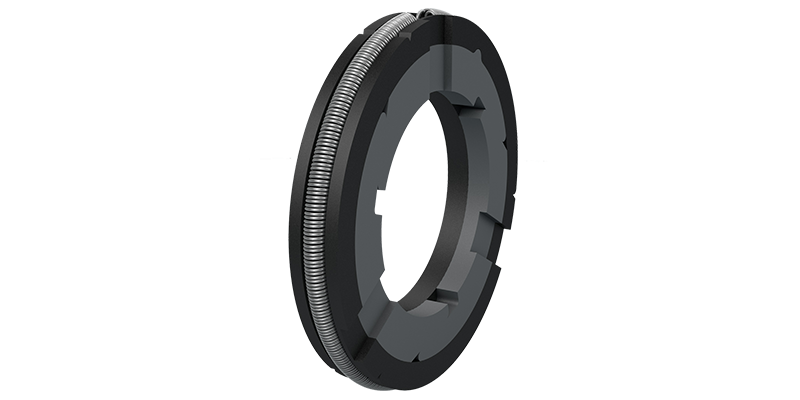
DESIGN ADVANTAGES
· Unique milled stop design eliminating pin breakage issues.
· Increased end gaps of the step tangent ring compared to a conventional ring without the risk of breakage of the thin tangent sections, due to the ring being held captive inside the outer tangent to rod ring.
· Outer tangent to rod ring covers the end gaps of the inner step tangent ring, effectively removing the leak path of the inner step tangent ring gaps.
FEATURES
· Double or single acting by use of face slots
· Suitable for all rod diameters and all gasses
· Inner step tangent ring keeps the assembly open, preventing the outer tangent to rod ring from closing in on itself
· Provides easy installation on the rod
· Controlled tests have shown the sealing performance to improve by at least 25% compared to conventional rings
· Available in mixed materials where the outer tangent to rod ring acts as an anti-extrusion ring
· Depending on operating conditions it may be possible to avoid an additional anti-extrusion ring
· Suitable for packing case designs with narrower seal grooves where axial length is limited
Radial load is shared between the inner and outer rings as the compressive gas force squeezes the outer tangent to rod ring resulting in:
· Improved sealing performance
· Lower friction
· Reduced heat generation
· Longer running life
Sales Bulletin: Emissionguard TR2
(EGTR.ENG.1809.LTR)
CPI manufactures to the highest quality standards a full range of pistons and piston rods in stainless or alloy steels, aluminum and cast iron, for a broad range of applications and operating conditions.
Experienced technical knowledge of compressor design and operation ensures that the optimum materials, surface treatments and sealing components are selected for each application.
FOR A WIDE RANGE OF OPERATING CONDITIONS
CPI manufactures to the highest quality standards a full range of pistons and piston rods in stainless or alloy steels, aluminum and cast iron, for a broad range of applications and operating conditions. Experienced technical knowledge of compressor design and operation ensures that the optimum materials, surface treatments and sealing components are selected for each application. FEA analysis is used to ensure the design meets all of the highest CPI engineered standards to guarantee product integrity and quality.
All pistons and rods are inspected to assess how to proceed with reconditioning and to ensure their suitability for re-use. Piston reconditioning may include re-machining of grooves and re-anodizing. Rod reconditioning may include machining, grinding, polishing and the application of specialized spray coatings. Finally, all parts are re-assembled including CPI piston and rider rings.
· Piston manufacturing
· Piston rod manufacturing
· Specialized thermal spray and plasma coatings
· Rolled or cut threads
· Piston and rod repair and reconditioning
· Manufacturing of piston and rider rings
· Tungsten carbide coating and five alloy coating available
With the ever increasing concern for the effects upon the global environment, systems to control emissions are becoming even more important. As part of its commitment to its customers and the environment, CPI has a range of purge control systems that maintain buffer pressure and monitor gas flow and packing condition to eliminate emissions from packing cases used in reciprocating compressors.
CPI has developed an advanced packing ring monitoring system offered in “MD” – Modular Design, “FD” – Fabricated Design and “FP” – Face Plate Design styles. The systems let you easily monitor packing ring life to ensure you are in compliance with fugitive emission standards. The MD Series monitors vent pressure, purge gas pressure, and purge gas flow on each cylinder stage individually. These three indicate the packing ring life. The FD Series incorporates multistage monitoring into one panel, eliminating the need for individual stage inspections.
CPI monitoring systems:
· Are designed and engineered for specific operating conditions, and are available for single or multiple units with automatic and manual operation.
· Are specifically designed to comply with present and future EPA Clean Air Act regulations, including standards for control of Volatile Organic Compounds (VOC) and Volatile Hazardous Air Pollutants (VHAP).
· Adheres to API 618 guidelines; provides saving through predictive maintenance scheduling; prevents costly emergency shutdowns.
· Has an optional “Bypass Start-up System” to put a quick seal on the purge gas side without operator adjustment during start up.
· Can be retrofitted to any existing packing case.
· CPI static seal provides the ideal solution to virtually eliminate gas leakage through the packing case when a compressor is inactive.
· Have all components engineered to meet or exceed industry standards.
CPI can convert your existing case to a purge design. Converting your packing case to a purge-gas system allows you to monitor your packing ring life and comply with tough emissions regulations.
At CPI we recognize that the specialized compressors used in the LDPE (low-density polyethylene) industry are highly evolved machines. CPI is responsive to the needs of this area of operation, having considerable experience in the design and manufacture of these specialized products to a high standard of quality, precision and with the use of appropriate materials for hyper packings, guide bushes, poppets, cups and plungers. In conjunction with users, we have been successfully involved in the development and installation of specialized designs for many specific applications. As part of these collaborations, we offer an option to manufacture parts using customers’ own unique designs and specific materials.
CPI operates a quality assurance system throughout all of its manufacturing plants which conforms with ISO9001.This discipline is rigorously applied to all hyper products recognizing the critical task which they must perform in service. To achieve this high standard of quality, CPI undertakes certain minimum procedures for all hyper products, including:
· Careful selection of raw materials, with supplier audits
· Chemical and mechanical certification of all raw material with full traceability
· Ultrasonic inspection of all raw materials for any internal defects
· Appropriate heat treatments and stress relieving to achieve specified tensile strength range and freedom from residual stresses
· Precise finish lapping to size and surface finish tolerances
· Magnetic particle inspection of the finished surfaces, where applicable
· Surface hardness and 100% finish inspection
· Full inspection report including documentary certification for all heat treatments and N.D.T. inspections
In addition to the manufacture and supply of components, CPI is committed to keeping compressors performing and maximizing operational availability. With this understanding and focus, CPI believes the supply of replacement parts is critical in achieving this. CPI is able to support operators around the clock; this also includes a comprehensive reconditioning service from many of our worldwide operations.
TO GET YOUR COMPRESSOR BACK UP AND RUNNING
In addition to the manufacture and supply of components, CPI is committed to keeping compressors performing and maximizing operational availability. With this understanding and focus, CPI believes the supply of replacement parts is critical in achieving this.
CPI Service is a rich resource for many compressor spare parts and also has specific facilities supplying parts for many of the markets we serve, especially the natural gas market. Experienced technicians will help select the right product, provide installation assistance and advice on upgrades, monitoring or compression processes.
Inventory of replacement components:
· Extensive stock in each location to meet operators’ needs
· Full line of parts to support operators as a “one stop shop”
· Database to provide instant, up-to-date information on location and availability
· Rapid delivery to ensure minimal downtime
· Same-day service available for numerous parts
· Custom sealing components manufactured accurately and efficiently
The strategically located network of CPI Service centers provides easy access to operators for a wide spectrum of compressor services such as:
· Reconditioning
· Repair services
· Replacement parts resource
· Field services
· Component manufacturing
· Specialist support and technical services
· Troubleshooting and proven problem solving solutions
CPI molds engineered plastic materials used in the reciprocating compressor industry. These materials include Nylon, PEEK and other proprietary blends. Blank sizes are held to close tolerances and pass several quality checks to exceed customer requirements. Over one hundred different blank sizes are currently available.
Today's advanced polymers have excellent mechanical properties and are capable of working at temperatures up to 400+ degrees F. In most cases, a simple conversion to low mass polymer sealing elements can give existing valves in reciprocating compressors a vastly increased life as well as reduced energy consumption and maintenance costs, without having to alter the valve body or modify the valve cage. The main advantages of polymer plates & rings over metallic are as follows:
· Heat resistance to impact fatigue
· Ability to operate at higher lifts
· High tolerance to dirt, liquids & chemicals
· Reduced wear to valve seat & guard
· Improved sealing capabilities
· Manufactured to exact size
· High stock availability
· One source for all your Peek, Nylon & Mid-Temperature valve plates
· Glass Filled Peek, Carbon Filled Peek
· Glass Filled Natural & Yellow Nylon
· Glass Filled Mid-Temperature Material
Sales Bulletin: Metallic and Non-Metallic Wear Products
(WEARPRODUCTS.1708.LTR)
The CPI name is synonymous with technological innovation. We are committed to proactively developing technologies that increase reliability and performance by creating special materials with unique problem solving capabilities.
CPI proprietary Special Polymer Alloys have been successfully applied to piston and rod sealing components, providing excellent reliability and efficient performance. These materials have enabled many compressor operators to achieve longer seal lives compared to other materials available. They have also made it possible for changes and improvements to compressor designs which have significantly improved reliability and reduced operating costs. CPI Special Polymer Alloys solved the problem of seal life in existing non-lubricated compressors. They are also used to convert lubricated compressors to non-lubricated operation in ways that were not previously possible with traditional filled PTFE materials.
Compression Molding
Standard filled PTFE grades are typically free sintered whereas the specialty alloys are hot compression molded.
Injection Molding
Thermoplastics such as nylon and PEEK are injection molded in high volumes or unique shapes.
Extrusion and Transfer Molding
Thermoplastics are also extrusion or transfer molded to achieve unique or complex part designs and large diameters that are not possible using traditional compression or injection molding techniques.
Sales Bulletin: Materials for Pump Wear Parts
(MPWP.1801.LTR)
Sales Bulletin: Sealing & Wear Products
(S&WP.1506.LTR)
CPI materials for pump wear parts (CPI Materials 182 & 183) are proprietary polymer alloys designed for pump bushing wear rings, guide bushings and thrust washers in liquid pumps.
The these exclusive polymers are intended to reduce diametral clearance on pump wear parts without the risk of damage to metal components. The properties of these materials are designed to help avoid catastrophic pump failures caused by dry-run start up or excessive vibration.
· Dry running tolerance
· Protection of pump shaft
· Reduced clearance minimize re-circulation
· Easy to machine, no treatment required
· Non-galling and non-seizing properties
· Low friction coefficient means long running life
· According to API 610
· Excellent chemical compatibility
Due to premature wear of many PTFE based bearings, CPI materials for pump wear parts are ideally suited for use in agitator and mixer bearings due to its chemical and frictional resistance, combined with excellent dimensional stability and improved running performance.
CPI materials for pump wear parts have a low coefficient of thermal expansion and provide excellent resistance to chemical attack as well as protection against impacts, thermal shocks, and hydrolysis. Applications using CPI materials significantly increase hydraulics, improving pump performance with reduction in energy consumption and reduced wear, which is reflected in maintenance and operating costs.
CPI materials for pump wear parts have been successfully installed and operate in line shaft bearings, impeller wear rings, thrust washers on vertical pumps - (single or multi-stage) barrel pumps, API, bearings on Archimedes screws and horizontal pumps.
Sales Bulletin: Materials for Pump Wear Parts
(MPW.1506A4)