Murphy by Enovation Controls
Drive your equipment integration into the digital age and achieve enhanced diagnostics, on-screen troubleshooting and increased user efficiency. Seamlessly integrate these modules with our rugged PowerView displays for total equipment control.
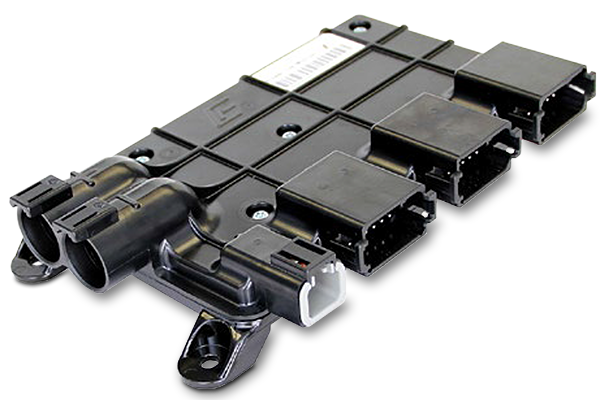
The Murphy Intelligent Xpansion Power Distribution Module (PDM) expands CAN bus control networks by replacing existing relay and fuse boxes with more reliable solid-state switches that can directly drive work lights, wiper motors, cooling fans, directional DC motors and other high current loads.
Each of the twelve (12) IX3212 outputs can switch, or proportionally control, up to 15 A loads in 2.5 A increments and feature built-in over-current detection and shut-down capability. Outputs are paired to run up to six electric motors with H-bridge direction control. Twelve digital inputs monitor switched battery, ground and floating inputs. Additionally, eight analog inputs are available with a 5V sensor supply.
The module is housed in a compact, sealed enclosure which can be mounted remotely on the equipment to greatly reduce wiring costs. For applications not requiring a CAN bus control, the inputs can directly trigger outputs without the need for a dedicated controller.
Sales Bulletin - IX3212
1311322 rev. 2017/01/24
Sales Flier - IX3212
1311316 rev. 2017/01
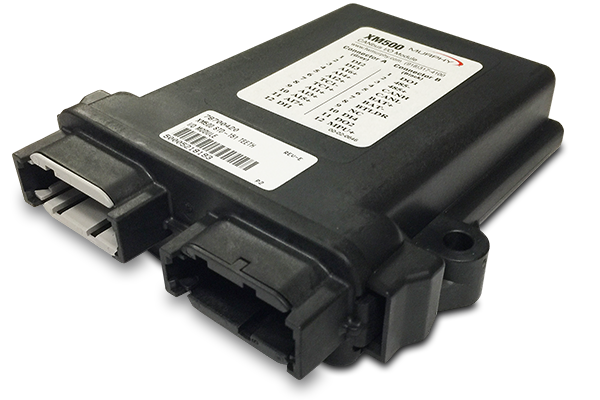
The XM500 module is a configurable Input/Output (I/O) module designed to bring analog and digital inputs and output onto the SAE J1939 CAN. The module can be configured to broadcast fault codes and activate digital outputs per input condition, some of which may not be provided by the OEM engine or transmission electronic control unit (ECU), such as fuel level, hydraulic oil pressure or a low engine coolant level switch.
Because the XM500 broadcasts information using the J1939 standard protocol, the information can be displayed using standard J1939 display modules, such as the PowerView 101. The XM500 configuration tool provides a user-friendly interface allowing the user to create or change the configuration used on the XM500 module.
Sales Bulletin - XM500
0710175 rev. 2014/09/27
Installation & Operations Manual - XM500 Configuration Tool
00-02-0789 rev. 2012/04/26
Standard Configuration/Wiring - XM500
0810278 rev. 2012/04/10
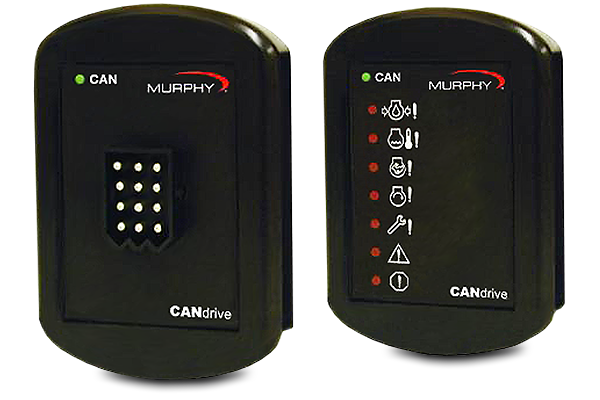
CANdrive modules read engine ECU CAN bus/J1939 data, drive standard electric panel gauges and provide LED indication of status and faults. CANdrive has three dedicated outputs for tachometer, oil pressure and coolant temperature gages, with DIP switch selectable compatibility for Murphy, VDO or Datcon gauges. For volume orders, the outputs can be custom configured for other gage types, lamps, relays or remote signaling. CANdrive offers a cost-effective instrument solution for modern electronic engines.
CANdrive is packaged in a compact, surface-mounted case with epoxy encapsulation for maximum durability and environmental sealing. Electrical connection is via a 12-way automotive type connector. Model CDV100F has a forward facing connector and one power/ CAN status LED. Model CDV300R has eight LEDs for indication of J1939-transmitted engine faults and status. All models include a six-way DIP switch for flexible configuration.
CANdrive advantages include:
· The retrofitting of existing electric gage panels to new J1939 compatible engines.
· The use of standard, economical electric gages with new J1939 engines.
· No need for installation of additional gage senders, tachometer magnetic pickups and wiring.
Sales Bulletin - CANdrive
0610067 rev. 2014/09/27
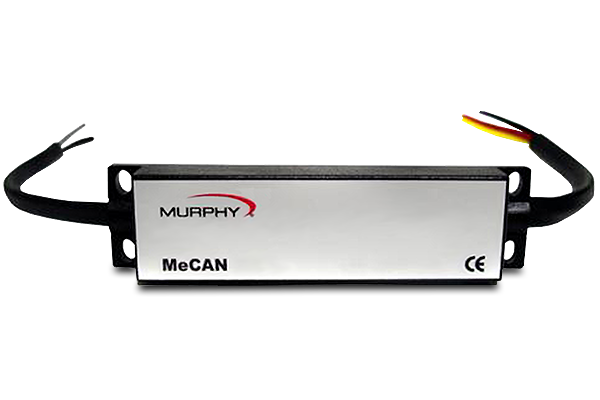
The MeCAN is a compact, encapsulated interface module that translates resistive sender, fault switch and speed signals into SAE J1939 CAN bus data. MeCAN allows quick and simple integration of mechanical engines into modern CAN bus systems. Applications include the retrofit of older engine meets with modern digital instruments, controls and telemetry, engine hour tracking and the development of standard control panels for mechanical engines. Input signals are translated into SAE J1939 CAN bus messages with assigned PGN address, data scaling and transmission rate. The output can drive an alarm lamp or buzzer or actuate a shut-down relay if the pressure, temperature or speed inputs deviate outside preset fault limits.
MeCAN has three sensor inputs and one output. Two inputs are for oil pressure and coolant temperature sensing, either by fault switches or resistive senders. The third input measures engine speed using a magnetic pickup or charge alternator signal. A fourth input is connected to a speed calibration potentiometer during set-up mode only. DIP switches allow selection of normal/set up mode and two speed input ranges. An LED gives indication of operating mode and CAN bus activity.
MeCAN is compact and light enough for inclusion in engine wiring harnesses but can also be surface mounted. The case is fully sealed in epoxy resin for high impact and environmental resistance. Two standard versions allow use with either fault switches or Murphy ES series resistive senders. Custom solutions are also available for non-standard, volume OEM requirements.
Sales Bulletin - MeCAN
0810332 rev. 2016/09/06
Installation Instructions - MeCAN
00-02-0665 rev. 2015/08
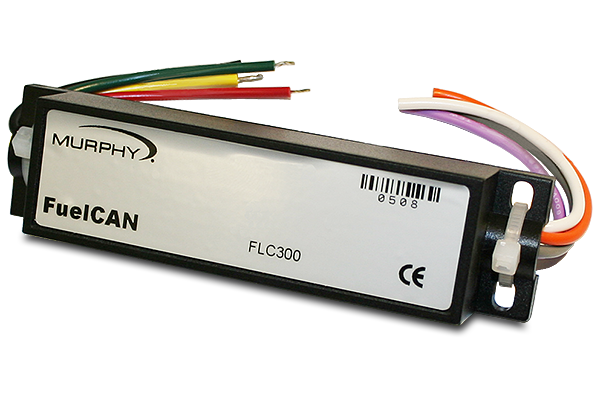
The FuelCAN is a compact interface that translates fuel level sender signals into SAE J1939 CAN bus messages. The device allows integration of standard senders into modern J1939/CAN bus engine instrument and control systems. FuelCAN inputs can also be factory configured for use with other types of fuel level or resistive senders. FuelCAN is compact and light enough to be incorporated into most wiring harnesses but can also be surface mounted.
FuelCAN modules have three inputs (only one of which is connected at any one time): input 1 is configured for use with Murphy ES series resistive fuel level senders; inputs 2 and 3 can be used with fuel level senders having compatible resistance ranges as shown below. FuelCAN inputs can also be factory configured for use with other types of fuel level or resistive senders. The polycarbonate case is fully sealed in epoxy resin for high impact and environmental resistance. A rear facing LED indicates input/CAN bus status.
Sales Bulletin - FuelCAN
0810308 rev. 2016/08/30
Installation Instructions - FuelCAN
00-02-0663 rev. 2015/08
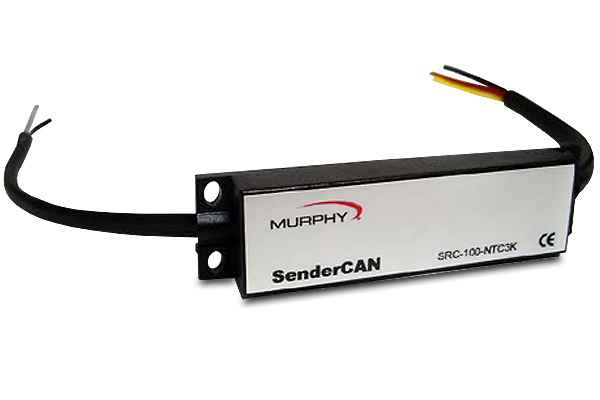
SenderCAN is a compact, encapsulated input & output module for J1939 CANbus systems. SenderCAN allows the integration of analogue and digital measurement, control and indicating devices into modern CAN and ECU-based engines and systems. SenderCAN has up to four inputs and two outputs, each of which is factory configured to OEM requirements. Inputs can be set for use with resistive sender or switch signals, which are translated into J1939 CANbus messages with appropriate PGN address, data scaling and transmission rate. Outputs can be configured to drive gauges, lamps, relays or other control devices, based on received J1939 data.
SenderCAN has up to four inputs and two outputs, each of which is factory configured to OEM requirements. Inputs can be set for use with resistive sender or switch signals, which are translated into J1939 CAN bus messages with appropriate PGN address, data scaling and transmission rate. Outputs can be configured to drive gages, lamps, relays or other control devices based on received J1939 data.
Standard versions are available for use with common senders, but SenderCAN is primarily intended for OEM-specified input, output and CAN bus requirements. SenderCAN is compact and light enough for inclusion in most wiring harnesses but can also be surface mounted. The case is fully sealed in epoxy resin for high impact and environmental resistance.
Sales Bulletin - SenderCAN
0810313 rev. 2016/09/06
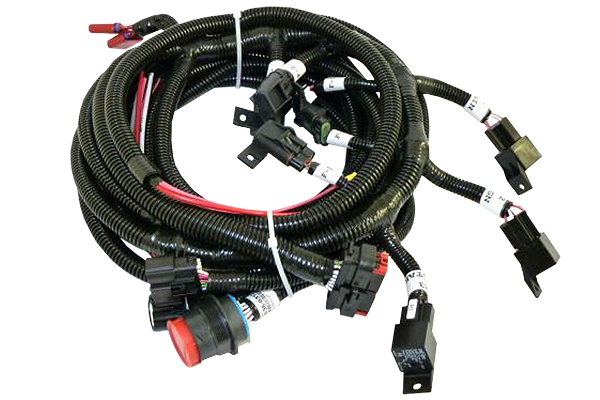
Murphy Industrial Harnesses bring universal connection to any engine. Harnesses are built to the specifications of each engine manufacturer and customer. When requesting the MIH Harness, specific information will be obtained so that the correct harness may be built for your engine.
Industrial Harness features:
· Connect any MurphyLink Panel to major engine manufacturers’ engines.
· Customizable per specific customer application and requirement.
· Standard 21-pin Deutsch connector interface.
· Built to strict quality standards for long-term reliability.
· Manufactured in the U.S.A.
Sales Bulletin - Industrial Harnesses
1211030 rev. 2017/01/25