Miratech Catalyst Services
Our goal is to provide you with the best possible catalytic services using state-of-the-art technology. Being part of Miratech's national distributor network provides a competitive advantage, as we can offer the full spectrum of catalyst management and scientific/analytical services. Our facility and technical staff monitors and analyzes the life cycle of your catalyst elements. We track each element by serial number and recommend a maintenance schedule which includes inspection and cleaning of your elements. We've made an investment to bring you a local, full-service catalyst chemical washing facility.
When necessary, we may draw upon the experience of the manufacturer. Miratech has extensive expertise in catalysis and nano-phase surface chemistry. They are uniquely qualified to evaluate catalyst life and associated performance. Their involvement includes non-destructive performance testing, chemical and physical analysis, and precious metal reclaim.
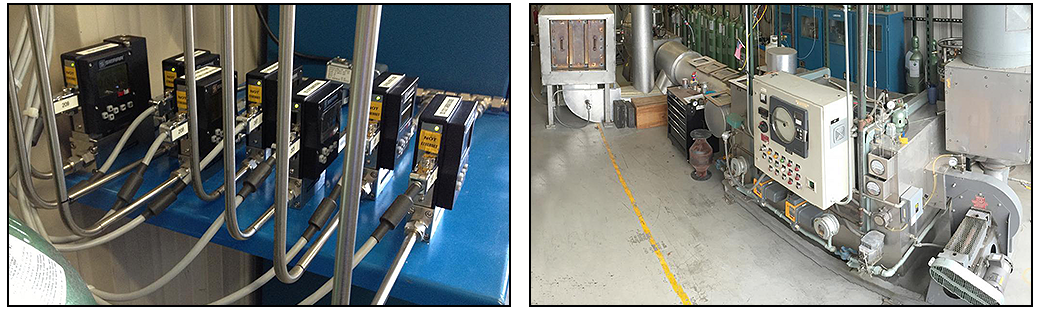
There are conditions that will deactivate or destroy the catalyst. Understanding how a catalyst deactivates, and avoiding those conditions, will ensure maximum performance and service life from the catalyst. The catalyst should be physically inspected at 6 to 12 month intervals for gas-fired systems with low loading of exhaust gas particulate and low oil consumption rate. Monthly inspections may be necessary for systems with high oil consumption, fuel containing high sulphur or other catalyst contaminants, and/or prone to misfires and over-temperature events.
The catalyst elements in reciprocating engine applications operate in an environment with known contaminants and potential elevated temperatures that will gradually decrease the destruction and removal efficiencies (DRE). Under normal operating conditions, the DRE will gradually decrease as a result of masking - a process by which contaminants deposit and accumulate on the catalyst surface.
Eventually, the accumulation covers the active surface area of the catalyst and prevents the exhaust gas from contacting the active precious metal sites. Even though the deposit may be too thin to effect a pressure drop, the performance will decline. Sulfated ash masking is the most common form of masking and is a product of the combustion of lubrication oil. Masking is often a reversible process in which the DRE can be restored with a chemical wash process.
Fouling occurs when solids physically plug the cells of the substrate and block gas flow through the catalyst. This can be caused by large particulate material in the gas stream or by deposition of an inorganic component (e.g. silica) and organic components (e.g. ash, carbon) as a by-product of combustion. Although the catalyst reduction performance may not be affected, disruption of exhaust flow through the catalyst causing high engine back-pressures will degrade engine performance and may result in engine stalls and high fuel consumption. When possible, the source of the fouling agent should be identified and corrected. A fouled catalyst can usually be restored by vacuuming or by chemical washing.
During your inspection, look for these common types of catalyst fouling:
Carbon Fouling - Carbon fouling is evident by a soft, sooty black deposit on the catalyst. These carbon deposits will eventually restrict flow and increase back pressure. They will also mask the active surface area of the catalyst resulting in degraded emission performance and reduced exothermic temperature rise. These carbonaceous deposits could ignite on the catalyst surface during an engine misfire. Carbon fouling originates from an overly rich air-fuel ratio.
Ash Fouling - Ash fouling is evident by a grayish-white powdery deposit on the catalyst that could accumulate to the point of plugging substrate cells. These ash deposits will eventually restrict flow, increase back pressure, mask the active catalyst surface area, and reduce emission performance. Ash fouling originates from an engine oil with high sulfated ash content, and can be exacerbated by an overly lean air-fuel ratio.
Oil Fouling - Oil fouling is evident by dark brownish-black coating on the catalyst and possibly the odor of crankcase oil. These oil deposits will eventually mask the active catalyst surface area and degrade performance, restrict air flow and increase back pressure, and cause high temperature alarms and shutdowns. Oil fouling originates from too much lube oil entering the engine exhaust gas.
Over-Temperature - Over-temperature often occurs within the core of the catalyst and may not be evident until damage is severe. Possible indications may range from a clean white, powdery appearance, to small pin-holes in the foil near the leading edge, to catastrophic incineration of the catalyst module. Over-temperature conditions originate in the engine from misfires, sticking exhaust valves, excessively lean air-fuel ratio, and other engine causes.
Certain materials can react with the active catalyst surface to form compounds or alloys that are not catalytically active. For example, lead and phosphorous can form alloys with platinum, forming a catalytically inactive metal, and reducing the performance of the catalyst. This process is usually irreversible - little can be done to rejuvenate a poisoned catalyst and replacement is usually necessary. Before replacing the catalyst, identify the poison contaminant(s) and eliminate the sources.
Known catalyst poisoning agents, that can cause irreversible loss of catalyst activity, include lead, mercury, arsenic, antimony, sodium, potassium, lithium, zinc, copper, tin, iron, nickel, chrome, silicon, phosphorous and fluorine. Common sources of poisoning agents include fuel (landfill gas, digester gas, refinery gas, arsenic-laden natural gas), lubrication oil, coolant, anti-freeze, RTV silicon and airborne contaminants. RJ Mann & Associates, Inc. partners with Miratech to offer analytical chemical testing to identify and quantify the presence of catalyst poison compounds.
Under normal engine operation, the catalyst exothermic temperature rise is 50-75°F for three-way catalysts, and 10-25°F for oxidation catalysts. Maximum post-catalyst temperature is 1250°F. In the event of a misfire, excessive concentrations of hydrocarbons and air generated from the cylinder(s) can lead to irreversible catalyst damage, if not quickly corrected. Misfires force the catalyst into an uncontrolled combustion mode, in which the catalyst combusts all the hydrocarbons the exhaust oxygen will support. The net result is an exothermic reaction elevating the catalyst temperature above the normal operating range, and sintering of the catalyst. Once sintering has occurred, catalyst pore volume and internal surface area are permanently lost and precious metal sites are permanently lost.
Note that even if the engine exhaust temperature is within the catalyst operating specification, if excessive unburned fuel reaches the catalyst, a large exotherm could occur within the catalyst itself, raise the catalyst core temperature, and sinter the catalyst element.
RJ Mann & Associates, Inc. works seamlessly with Miratech to provide you with the most comprehensive suite of catalytic services in the industry. We also support the best catalyst element guarantee, covering both emission reductions and mechanical element integrity.